Wishing to implement a barcode system for your warehouse for online selling, this article can help you to simplify the planning and implementation.
Implementation of a barcode system in the organisation should be the first requirement for most of the warehouses in the company. However in our country Malaysia, this task is not well performed especially for the company setup before 1980. However we help you to summarize what you suppose to do before implementing this.
Step 1 product category and grouping
In order to implement the barcode system, the first thing you need to do is know your product category and characteristics. This is the most important business skill you must have in order to implement proper warehousing. Are you selling the item in custom form or you are selling the item in a proper predefined pack? If you are selling the product in custom form then the most important step you need to do is custom the cash and carry format to predefined form or else you need to request someone to handle this tedious process during the warehousing daily as standard operating procedure (SOP).
Step 2 Warehouse Location definition
Second rule of implementation in barcoding in the warehouse is the proper naming of location for your warehouse. Some organizations have more than one warehouse in same state or different state, the warehouse may be located near to each other or some of them may be located a few hundred kilometers away. Proper naming and reserve of future warehouse expansion is something that needs to be considered before you give a proper naming for your warehouse. Examples of warehouse naming include WH001, WH002, WH003, and so on. Same characters length of warehouse name will help to make your barcode look nice, more tidy, same length and size. (if you are using 1D barcode)
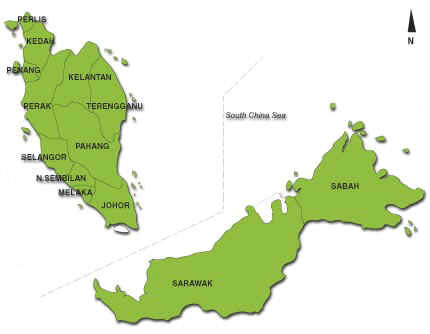
Step 3 Warehouse shelf naming and category
Fixed shelving or bins systems are important for easy locating and easy picking. The fixed numbering also makes it easier to implement. Dynamic shelving or bin is today's latest technique used with the introduction of automated shelf robots. Dynamic or moving shelf systems simplify the picking process and allow the higher efficiency of picking in the warehouse.
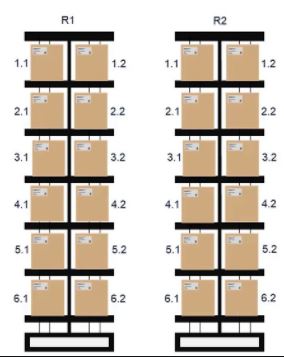
Step 4 product numbering
After the above numbering system, the product number is the most important aspect to be considered during the barcoding system. Once the inventory volume increases, generating barcode tags can be a heavy task for the warehouse staff. In order to simplify the future task, reuse existing printed barcode numbers is one of the most important considerations that must be considered during the product numbering process. If your company is selling Fast Moving Consumer Product (FMCG), the EAN13 barcode and ITF14 barcode is the ideal barcode you can use instead of regenerating your own barcode number.
.JPG)
Step 5 Using barcode, RFID or Vision?
RFID is a hot topic in the Automatic Data Capturing arena, Vision even better compared with RFID and barcode. However at this moment of time, the cost and technology to implement RFID or vision in the warehouse is still not economical compared with the barcode solution especially in South East Asia due to the manpower cost, technology maturity and the working culture. so you may temporarily forget about RFID and Vision technology.
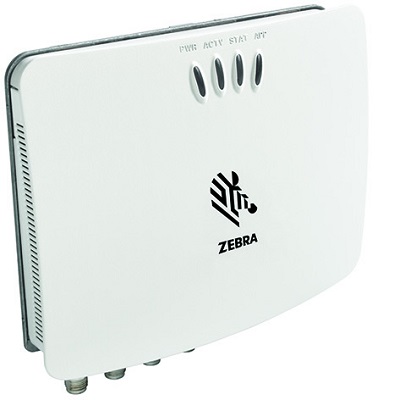
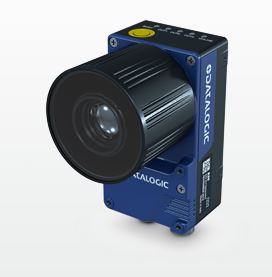
Step 6 Using 1D or 2D barcode?
Using 2D barcode technology should be the first consideration if you required to generate your own barcode, the main reason to use 2D barcode is because 2D barcode required small space compare with 1D barcode. At the same time the printhead wear and tear or replacement can be longer compared with 1D barcode. In term of long run, it have better saving compare with 2D barcode.
Step 7 Selecting the correct label generating device.
A barcode sticker printer is the most economical way at this moment to generate barcodes in the long run. Daily printing quantity and label size is one of the main considerations when you decide your label sticker printer.
Step 8 Selecting the correct label size
The correct sticker size helps you to minimize the running cost in the long run. The smaller the label, the cheaper the size. If you can select the standard size in the Malaysia market like 40mmx 20mm label, 60mm x 30mm label, it helps you to reduce the cost even further.
Step 9 Selecting the correct ribbon size.
Once you have fixed the label size, now is the time to select the correct ribbon size, the ribbon size normally bigger than the ribbon size in order to give more protection for your printer printing element. Of course the correct ribbon material also gives you a different result on the printout quality and long lasting effect.
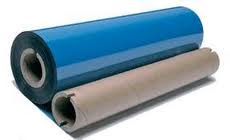
Step 10 Barcode scanner for reading purpose
After the barcode is printed, it comes to reading the barcode back to your inventory control system. A good performance scanner can give you minimum reading time during the scanning operation. Top brand barcode scanners like Zebra, Honeywell and Datalogic scanner give you the 100% confirm no mistake and consistent reading performance when you scan the printed barcode.
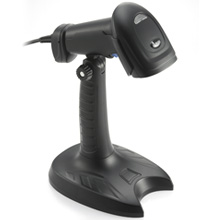
By:
annie
| Date:
11 Jun2021