Industrial container (totebox) tracking makes simple with barcode or RFID technologies.
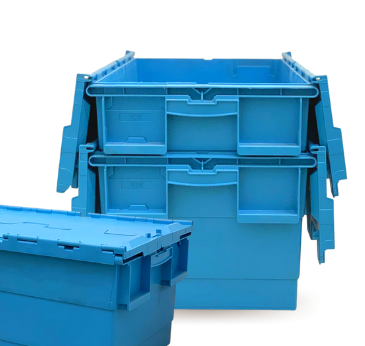
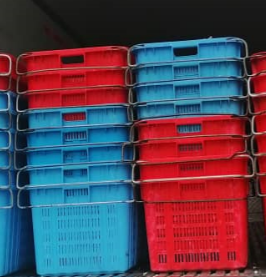
Introduction
The process of tracking industrial distribution containers (totebox) involves several steps and technologies to ensure efficient and accurate monitoring of their movement and location throughout the supply chain. However, this tracking should not and must not add in too much task for the warehouse worker. Here's a 6 steps breakdown of the key steps involved:
1. Container Identification:
.jpg)
Assign unique identifiers, such as barcodes or RFID tags, to each container.
Place these identifiers in visible and accessible locations on the container.
Ensure the identifiers are durable and can withstand harsh environmental conditions.
You may apply additional protection for the barcode or RFID tags.
2. Container Scanning and Data Capture:
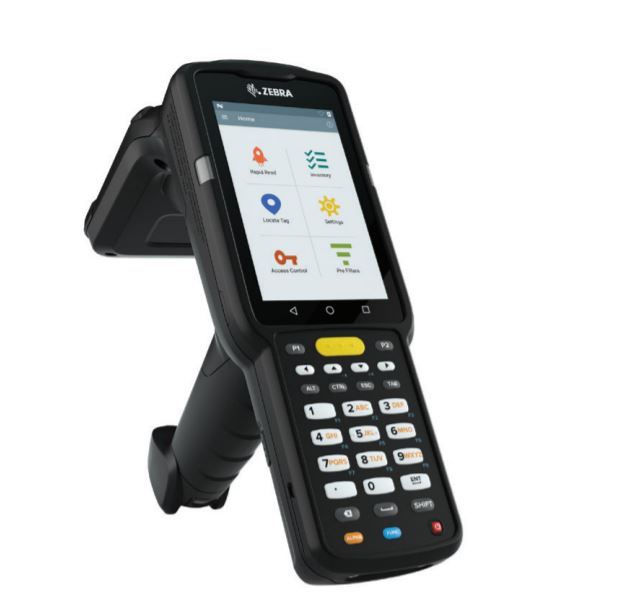
Implement scanning infrastructure at strategic points in the supply chain, such as warehouses, distribution centers, and transportation hubs.
Utilize barcode readers or RFID tag readers to capture the unique identifiers of containers as they pass through these locations.
Integrate data capture devices with AGen Totebox management systems to store and update container location information.
3. Real-time Tracking and Monitoring:
.jpeg)
AGen totebox centralized tracking system that collects and processes data from various scanning points.
Provide access to tracking information to authorized personnel to make informed decisions regarding totebox inventory management, transportation logistics, and customer deliveries.
4. Exception Handling and Alerting:
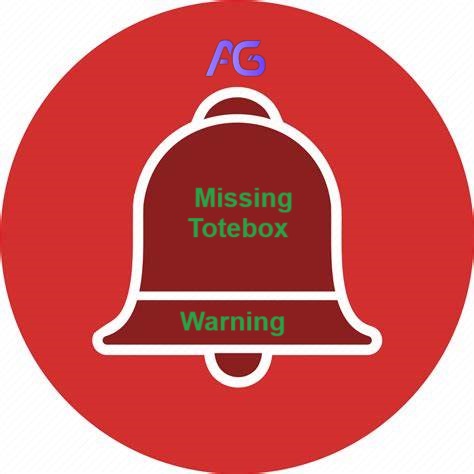
Establish thresholds and triggers for container movement patterns and expected arrival times.
Set up alerts to notify personnel of any deviations from expected container movements or delays.
Implement procedures for investigating and resolving any discrepancies or exceptions in container tracking data.
5. Data Analytics and Reporting:
Analyze historical tracking data to identify trends, patterns, and potential areas for improvement in container movement efficiency.
Generate reports that provide insights into container utilization, dwell times, and overall supply chain performance.
Use data-driven insights to optimize container allocation, streamline transportation routes, and enhance supply chain visibility.
6. Continuous Improvement and Innovation:
Regularly review and evaluate the tracking process to identify opportunities for improvement and optimization.
Adapt tracking procedures and software to accommodate changes in supply chain dynamics, customer requirements, and industry regulations.
Summary
Industrial distribution containers (totebox) are tracked using a combination of unique identifiers, scanning infrastructure, AGen tracking software, and data analytics. The process involves assigning identifiers to containers, capturing their location data, monitoring their movement, identifying exceptions, and using data to improve efficiency.
By:
pang
| Date:
23 Nov2023