Ship and tanker component tracking while sending for repairing, tracking solution with Autotrack to make your component tracking easy with the use of 2D QR barcode.
Introduction
Shipping industry is one of the important industries in Malaysia. This commercial activity made the ship repairing industry become part of the important service industry in the coastal site of Malaysia port.
Challenge faced by the industry in tracking.
The main challenge faced by the industry on tracking the part or component of the ship or vessel is the service time for repairing a ship is too long. During this long period of serving time, the ease of retrieving records is one of the main concerns of the industry. Some repairing parts may use up to 6 to 12 months time for servicing or repairing. If the servicing company does not have proper records for the tracking process, it may cause a long unwanted process in finding back the servicing part.
Example of components to be tracked during the servicing process.
In one shipyard service or repair center for big ships, merchant ships, oil tankers, cargo ships, bulk carriers, container ships, passenger ships, navy ships or etc. Every component in the ship body will need a certain level of maintenance or repair due to wear and tear or sea water corrosion. The sample or part required for the shipyard maintenance department to repair the part include steam turbine, ship engine, bedplate, entablature, oil sump, servo oil rark, fuel valve pipe, exhaust valve and other available parts in the ship.
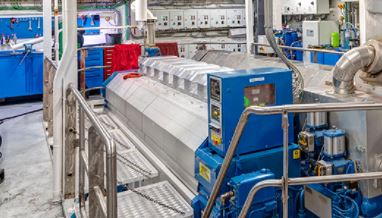
How does autotrack asset tracking help to simplify the tracking?
Once the servicing parts of the ship component is taken down from the ship, each component will be assigned with the 2D QR barcode. different parts will be delivered to different process examples like blasting and painting, carpentry job, machining services, mechanical services, electrical services, hydraulic services, CNC repairing depending on the faulty condition. If the maintenance task can be performed onsite, then the repaired parts will be installed back to its main compartment after repair, else the parts will be sent to a 3rd party repair center. Every repair task may involve more than one 1 part and the process may take more than 6 months. During the waiting period, the autotrack will automatically send out reminder emails to the person in charge in order to follow up the servicing status with different repair centers. It also gives the overview of the repair item. Before and after the repair photo will be kept for reference purposes in order to be proof for the customer reference purposes.
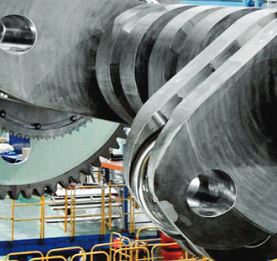
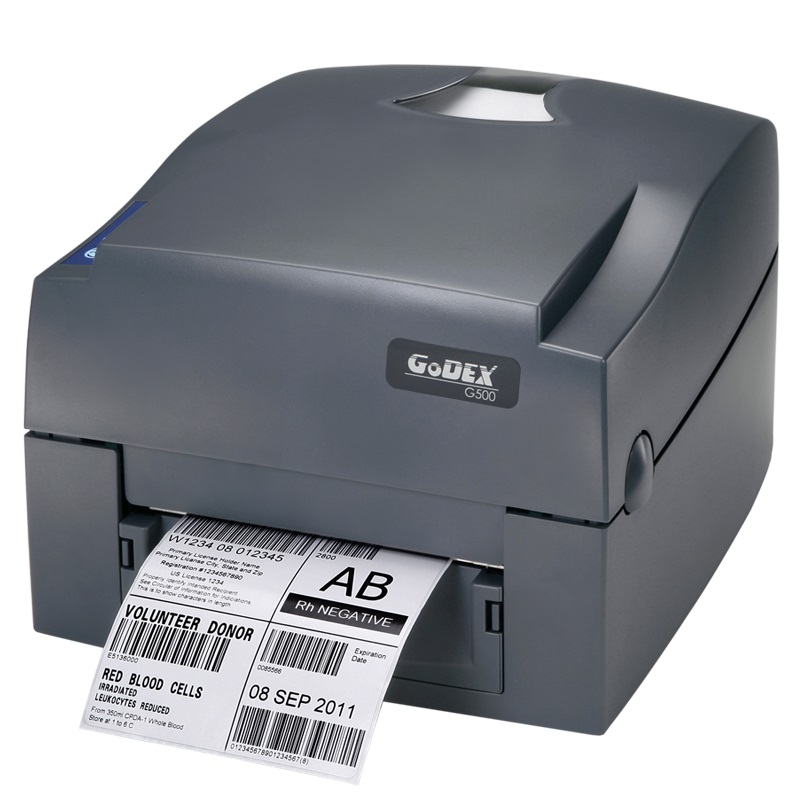
Part involve in the tracking
Autotrack Enterprise Asset Tracking (Optimise for tools tracking purpose)
2D QR barcode printer
2D QR barcode heavy duty sticker
Mobile Phone
By:
pang
| Date:
15 Sep2021